Principle and application development trend of 3D camera vision system
With the upgrading and transformation of automation, industrial robots are more and more widely used in manufacturing, logistics and other fields. We can see industrial robots working meticulously everywhere in the factory. As the “eye” of industrial robots, 3D vision has become a key factor affecting the application and performance of industrial robots. Therefore, the importance of 3D vision can be seen, and high-precision 3D cameras have become the favorite in the industrial field.

Speaking of cameras, we are probably familiar with them. So, what’s the difference between 3D cameras and common 2D cameras?
As the name implies, 3D cameras allow us to obtain the spatial information of the physical world, that is, three-dimensional physical information, which is one dimension more than 2D. 3D sensors are usually composed of ordinary 2D cameras and depth sensors. The algorithm is used to collect spatial information, which is generally composed of spatial point sets (X, Y, Z), namely point clouds. Yn ogystal, you can also output depth maps and brightness maps. In the industrial field, it is usually used in high-precision product detection and space disordered sorting processes.
1. Product testing
With the increase of labor cost, the contradiction of low detection efficiency is more and more obvious. At this time, many automatic detection technologies appear in our vision. While improving efficiency rapidly, people quickly found the second problem. The secondary injury caused by detection not only reduces the yield, but also causes a lot of waste. With the appearance of machine vision non-contact detection mode, the problem has been well solved.
2. Disordered sorting
The machine vision sorting system adopts the automatic operation mode of the assembly line used in mass production. The automatic sorting system is not limited by climate, time, human physical strength, etc., and can operate continuously. The automatic assembly line conveys products of different sizes and shapes to the camera in turn.
The camera transmits the data to the robot and places them in different trolleys according to the product shape and size. The sorting robot detects, extracts, recognizes and tracks the moving objects in the image sequence through visual tracking, and obtains the moving track of the object, so as to further process and analyze to realize the understanding of the object behavior and complete higher level tasks. The sorting robot can greatly shorten the delivery cycle of express delivery and improve the service level.
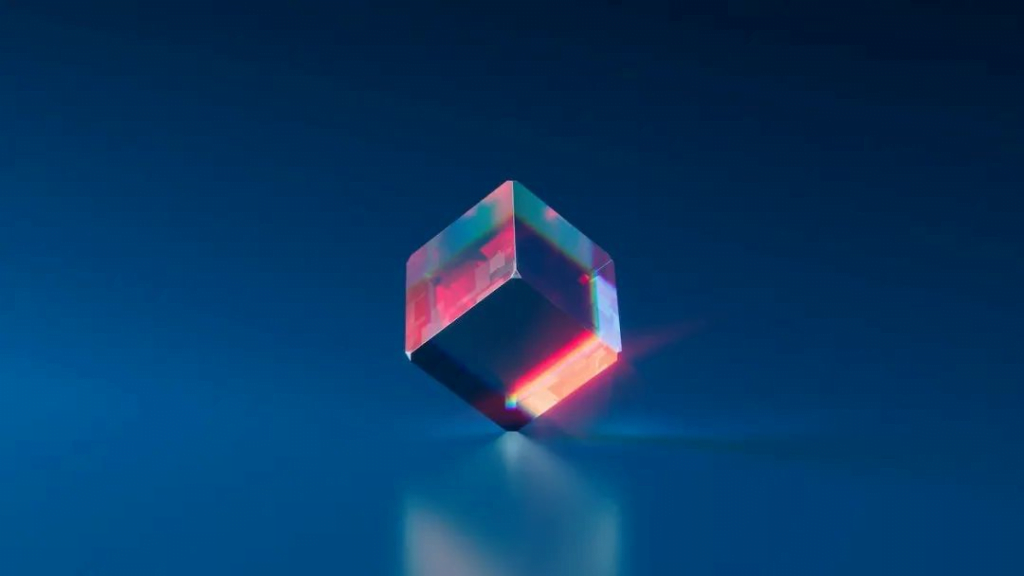
At present, in our domestic applications, we mainly divide 3D vision into laser triangulation, structured light, TOF light and spectral confocal.
Laser triangulation
Usually, a laser emitter is used to emit laser, and a camera is used to collect the reflected light, and the 3D contour data of the target object is analyzed through algorithm. Because the laser scanning is the reason, this detection method is more suitable for the high-precision and high-speed detection mode of the production line.
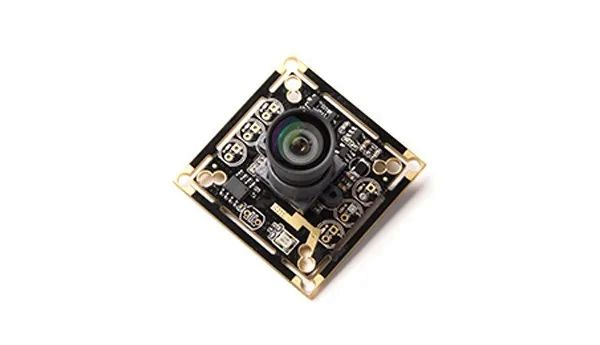
Laser triangle reflection is the laser emitted by the laser transmitter. The measured object moves through the laser beam. The built-in camera receives the reflected laser and calculates the 3D contour data. Because it depends on objects moving relative to the laser, this means it is very suitable for products on the conveyor belt.
Structured light
The structured light generated by the light source, which contains optical coding information, shines on the surface of the object to be detected. According to the deformation of the optical coding pattern, we can analyze the surface model of the object, and calculate the distance, shape, size and other information at the same time. We are more familiar with the application of vision guided robots.
TOF light
The distance of the target is determined according to the reflected light time difference received by the sensor through the high-speed transmitted optical pulse.
Spectral confocal
Based on the basic principle of optical dispersion, the relationship between distance and wavelength is calculated, and the position information of the target object can be easily obtained through the spectrometer decoding.
Machine vision can be said to be the lowest infrastructure layer of artificial intelligence. Among the main application fields of artificial intelligence industry, machine vision has a very deep and many application fields. From the perspective of the panorama of the entire industry chain, China’s artificial intelligence industry is in a rapid ecological construction period.
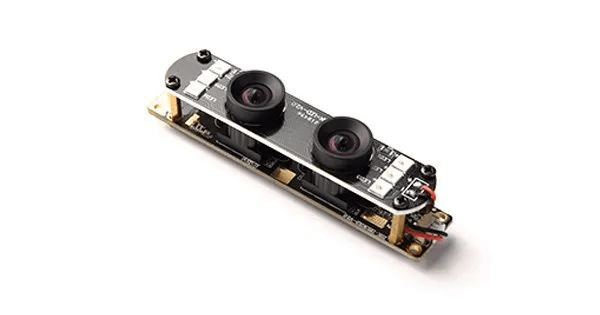
From the perspective of the whole field of machine vision, it is in a rapid reconstruction period. From the perspective of market analysis, machine vision is not a particularly emerging field. From the earliest image processing to the present, there are many large manufacturers in the market who have made long-term efforts in intelligent security and transportation. In the future, there will be greater opportunities in security, transportation, finance, consumer electronics and other fields through favorable policies in artificial intelligence. This is the application industry direction that the machine vision field focuses on.
Mae Shenzhen Jinshikang Technology Co., Cyf
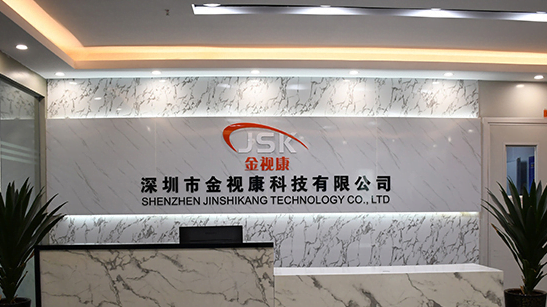
Founded in 2015, it specializes in providing various camera module products such as monocular and binocular cameras. After years of development, it has accumulated profound experience in video capture, video intelligent analysis, and vehicle electronic technology.
It has independently developed various differentiated camera modules such as object recognition, face recognition, iris recognition, and is widely used in new retail, face recognition, intelligent monitoring, industrial applications, and various image schemes. JSK is a high-tech enterprise integrating R&D, production, sales and service. Its products are sold at home and abroad and become the designated supplier of many listed companies. Relevant module products can be customized and developed according to the actual requirements of customers. Welcome camera module manufacturers and partners to visit our company and discuss cooperation.